The European Space Agency (ESA) is showing 3D-printed metal parts made onboard the International Space Station using a printer and materials the agency sent earlier this year. While 3D printing onboard the ISS is nothing new, the printing of metal parts in space is an important advancement. The agency’s goals are to be able to produce more tools and spares in situ rather than having to rely on resupply missions. An ambitious idea being pitched is to use captured space debris as input as well, which would further decrease the ISS’s dependence on Earth and expensive cargo runs from the bottom of the gravity well.
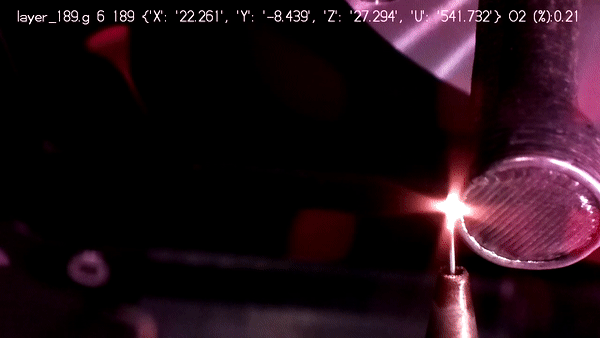
The 180 kg 3D printer lives in the European Drawer Rack Mark II inside ESA’s Columbus module. Controllers on Earth managed the printing process after installation. The printer ran for about four hours a day, with each layer inspected before continuing. This means the printing process took days, but running the machine continuously would, of course, cut printing time significantly.
The printer uses stainless steel wire that is fed to the printing location, where a laser melts it. As the pool of molten metal moves away from the laser-heated spot, it solidifies like plastic does in a regular FDM printer. Of course, with the melting point of stainless steel being around 1400 °C, it runs a lot hotter and thus requires that the printer to be inside a completely sealed box, with the atmosphere inside vented into space and replaced with nitrogen prior to starting the printing process. The presence of oxygen would totally ruin the print.
We badly want a practical metal printer for home use, but, so far, they remain out of reach. When you do get them, you might consider that there are different design rules for metal-printed parts.