
[ad_1]
Bryson DeChambeau is golf’s mad scientist. There’s nothing he won’t try if he thinks it could improve his game. Using a protractor on the course to read greens? Check. Brain training to achieve parasympathetic states conducive to good golf? Uh huh. Letting the composition of the flagstick determine whether he leaves it in or not for a putt? Sure, why not.
This is a guy who once borrowed his high school physics textbook from the library and copied it word-for-word. So, when he showed up at The Masters in April with the first 3D-printed irons ever used on the PGA Tour, people noticed.
Now, a couple of months later, coming off a second-place finish at the PGA Championship last month and following a three-under-par opening round of 67 at this week’s U.S. Open, DeChambeau’s irons are back in the spotlight—because they appear to be working.
How 3D-printed irons are different
DeChambeau’s irons were made by boutique clubmaker Avoda Golf. But aside from being 3D printed, they’re different from traditional irons in one crucial way.
The club face on drivers, woods, and hybrids is slightly curved to reduce sidespin and increase accuracy on off-center strikes. Irons are traditionally flat-faced to allow for predictable launch angles and consistent spin rates. DeChambeau’s 3D-printed irons feature a curved face, so they hit more like a hybrid than a traditional iron.
DeChambeau is known for his big swings and tremendous club-head speed. When hitting his old irons, he told the Golf Channel ahead of the U.S. Open, even the slightest mishit was causing his ball to either hook to the left or slice to the right (amateurs, you’re not alone). His high club-head speed exacerbated that effect. “So, I created curvature on the toe and the heel to get it started a little farther right on the toe and on the heel start it a little farther left so it makes sure it doesn’t go too far offline,” he said. “Much like the driver.”
In his first event using the clubs at The Masters in April, DeChambeau shot a first-round 65, leading the tournament at one point and finishing tied for sixth. And his recent strong showings prove that, with his new irons, DeChambeau the golfer is catching up to DeChambeau the entertainer.
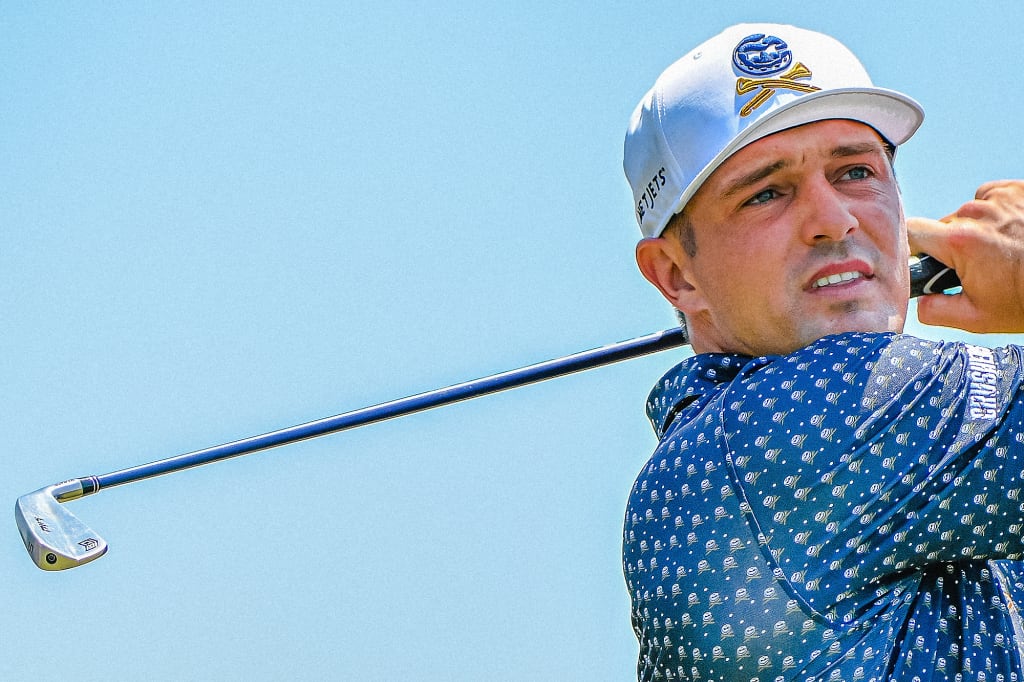
So, why 3D printing?
Prototyping golf clubs is tedious and expensive. The precision engineering required and the iterative process of creating multiple prototypes, testing, and making incremental adjustments based on feedback from players and data analysis don’t help.
DeChambeau envisioned his new iron design as far back as 2020, and it took about six months of development with Avoda to develop to design the clubs that met USGA guidelines. While it’s unclear how many iterations DeChambeau went through before settling on the design he ultimately debuted at The Masters, the speed of the 3D printing process compared to traditional methods means manufacturers are no longer tied to generic, mass-produced designs. With 3D printing, they can iterate quickly and experiment with new designs without incurring the traditional cost of prototyping.
According to Desktop Metal, one of the world’s leading 3D printing hardware manufacturers, prototyping golf club heads with 3D printing can reduce cost-per-part by 82% compared to traditional methods.
The result? Better, faster, less expensive, and more customized club design.
How much do they cost?
If you’ve read this far and you’re thinking about getting your hands on a set of DeChambeau’s 3D-printed irons, they’ll set you back about $10,000. But, as with any successful innovation, competitors are getting in on the action.
Just last week, Cobra Golf released the first commercially available 3D-printed irons. Limited to 500 sets, the heads retail for $3,000 and can be paired with a wide selection of aftermarket shafts and grips. It was inevitable that competitors like Cobra would Avoda’s lead, but the accessibility of 3D printing to the masses—however far off that may be—has the potential to change club-making, and the game of golf, forever.
The future of golf?
In fact, DeChambeau sees a world in which, one day, amateur golfers can prototype and develop their own custom clubs.
“Imagine having a 3D printer at your house, and you just print your own iron or do whatever,” DeChambeau said this week. “You can put it together and go hit it that afternoon. That’s really cool, compared to having a six-month process of prototyping it out and measuring it up and doing a couple iterations—maybe one of them is right, one of them is wrong—but you just 3D print, in an hour or so, a metal head and you stick a shaft on it and you go hit it.”
While we’re not there quite yet, one thing is clear: If Dechambeau continues to play at a high level, other players will inevitably play copycat, competing manufacturers will jump on Cobra and Avoda’s innovation train, and 3D-printed clubs will inevitably become a mainstay at a pro shop near you.
“Those days are coming,” DeChambeau said. “I don’t know how quickly it’s coming, but it’s certainly a really cool technology that we utilize, and hopefully it gets more widely known. Because that is the future.”
[ad_2]