Ever needed a strong yet adhesive-free way to really stick PLA to glass? Neither have we, but nevertheless there’s a way to use aluminum foil and an IR fiber laser to get a solid bond with a little laser welding between the dissimilar materials.
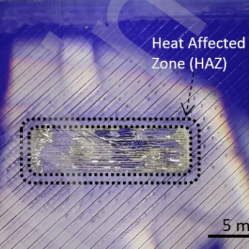
It turns out that aluminum can be joined to glass by using a pulsed laser process, and PLA can be joined to aluminum with a continuous wave laser process. Researchers put them together, and managed to reliably do both at once with a single industrial laser.
By putting a sacrificial sheet of thin aluminum foil between 3D printed PLA and glass, then sending the laser through the glass into the aluminum, researchers were able to bond it all together in an adhesive-free manner with precise control, and very little heat to dissipate. No surface treatment of any kind required. The bond is at least as strong as any adhesive-based solution, so there’s no compromising on strength.
When it comes to fabrication, having to apply and manage adhesives is one of the least-preferable options for sticking two things together, so there’s value in the idea of something like this.
Still, it’s certainly a niche application and we’ll likely stick to good old superglue, but we honestly didn’t know laser welding could bond aluminum to glass or to PLA, let along both at once like this.